Chemische Injektionsleitungen im Bohrloch – Warum versagen sie?Erfahrungen, Herausforderungen und Anwendung neuer Testmethoden
Copyright 2012, Society of Petroleum Engineers
Abstrakt
Statoil betreibt mehrere Bereiche, in denen die kontinuierliche Injektion von Ablagerungsinhibitoren in das Bohrloch angewendet wird.Ziel ist es, die obere Leitung und das Sicherheitsventil vor (Ba/Sr) SO4 oder CaCO zu schützen;Maßstab, in Fällen, in denen es schwierig und kostspielig sein kann, den Maßstab regelmäßig durchzuführen, z. B. bei der Anbindung von Unterwasserfeldern.
Die kontinuierliche Injektion von Ablagerungsinhibitor in das Bohrloch ist eine technisch geeignete Lösung zum Schutz der oberen Verrohrung und des Sicherheitsventils in Bohrlöchern, bei denen oberhalb des Produktionspackers Ablagerungspotenzial besteht.insbesondere in Bohrlöchern, die aufgrund der möglichen Ablagerungen in der Nähe des Bohrlochs nicht regelmäßig abgequetscht werden müssen.
Bei der Gestaltung, dem Betrieb und der Wartung der chemischen Injektionslinien muss besonderes Augenmerk auf die Materialauswahl, die chemische Qualifizierung und die Überwachung gelegt werden.Druck, Temperatur, Strömungsverhältnisse und Geometrie des Systems können den sicheren Betrieb erschweren.Bei den mehrere Kilometer langen Injektionsleitungen von der Produktionsanlage zur Unterwasservorlage und bei den Injektionsventilen unten in den Bohrlöchern wurden Herausforderungen festgestellt.
Es werden Felderfahrungen besprochen, die die Komplexität kontinuierlicher Bohrlochinjektionssysteme im Hinblick auf Niederschlags- und Korrosionsprobleme zeigen.Laborstudien und Anwendung neuer Methoden zur chemischen Qualifizierung sind vertreten.Der Bedarf an multidisziplinären Maßnahmen wird berücksichtigt.
Einführung
Statoil betreibt mehrere Felder, in denen eine kontinuierliche Injektion von Chemikalien in das Bohrloch angewendet wird.Dabei handelt es sich hauptsächlich um die Injektion von Kesselsteininhibitor (SI), wobei das Ziel darin besteht, das obere Rohr und das Sicherheitsventil im Bohrloch (DHSV) vor (Ba/Sr) SO4 oder CaCO zu schützen;Skala.In einigen Fällen wird ein Emulsionsspalter in das Bohrloch injiziert, um den Trennprozess so tief wie möglich im Bohrloch bei einer relativ hohen Temperatur zu starten.
Die kontinuierliche Injektion von Ablagerungsinhibitor in das Bohrloch ist eine technisch geeignete Lösung, um den oberen Teil der Bohrlöcher zu schützen, der oberhalb des Produktionspackers Ablagerungspotenzial aufweist.Eine kontinuierliche Injektion kann insbesondere in Bohrlöchern empfohlen werden, die aufgrund des geringen Skalierungspotentials im nahen Bohrloch nicht gequetscht werden müssen.oder in Fällen, in denen es schwierig und kostspielig sein kann, Kalkablagerungen regelmäßig durchzuführen, z. B. bei der Anbindung von Unterwasserfeldern.
Statoil verfügt über weitreichende Erfahrungen mit der kontinuierlichen Injektion von Chemikalien in Topside-Systeme und Unterwasserschablonen, die neue Herausforderung besteht jedoch darin, den Injektionspunkt tiefer in das Bohrloch zu verlegen.Das Entwerfen, Betreiben und Warten der chemischen Injektionslinien erfordert eine besondere Konzentration auf mehrere Themen.wie Materialauswahl, chemische Qualifizierung und Überwachung.Druck, Temperatur, Strömungsverhältnisse und Geometrie des Systems können den sicheren Betrieb erschweren.Es wurden Herausforderungen bei langen (mehrere Kilometer langen) Injektionsleitungen von der Produktionsanlage zur Unterwasservorlage und in die Injektionsventile unten in den Bohrlöchern festgestellt;Abb.1.Einige der Einspritzsysteme haben planmäßig funktioniert, andere sind aus verschiedenen Gründen ausgefallen.Es sind mehrere neue Feldentwicklungen für die chemische Injektion im Bohrloch (DHCI) geplant.Jedoch;In einigen Fällen ist die Ausrüstung noch nicht vollständig qualifiziert.
Die Anwendung von DHCI ist eine komplexe Aufgabe.Es umfasst die Fertigstellung und das Bohrlochdesign, die Bohrlochchemie, das Topside-System und das chemische Dosierungssystem des Topside-Prozesses.Die Chemikalie wird von oben über die Chemikalieninjektionsleitung zur Komplettierungsausrüstung und nach unten in das Bohrloch gepumpt.Daher ist bei der Planung und Durchführung derartiger Projekte die Zusammenarbeit mehrerer Disziplinen von entscheidender Bedeutung.Es müssen verschiedene Überlegungen berücksichtigt werden und eine gute Kommunikation während des Entwurfs ist wichtig.Beteiligt sind Verfahrensingenieure, Unterwasseringenieure und Fertigstellungsingenieure, die sich mit den Themen Bohrlochchemie, Materialauswahl, Durchflusssicherung und Produktionschemikalienmanagement befassen.Die Herausforderungen können darin bestehen, dass die Chemikalien in der Pistole sprühen oder in der Temperaturstabilität, Korrosion und in einigen Fällen durch einen Vakuumeffekt aufgrund lokaler Druck- und Strömungseffekte in der Chemikalieneinspritzleitung.Hinzu kommen Bedingungen wie hoher Druck, hohe Temperatur, hohe Gasgeschwindigkeit, hohes Ablagerungspotenzial,Große Entfernungen zwischen Versorgungsleitungen und tiefe Einspritzpunkte im Bohrloch stellen unterschiedliche technische Herausforderungen und Anforderungen an die eingespritzte Chemikalie und das Einspritzventil dar.
Ein Überblick über die in Statoil-Betrieben installierten DHCI-Systeme zeigt, dass die Erfahrungen nicht immer erfolgreich waren (Tabelle 1). Es werden jedoch Planungen zur Verbesserung des Einspritzdesigns, der chemischen Qualifikation, des Betriebs und der Wartung durchgeführt.Die Herausforderungen variieren von Bereich zu Bereich, und das Problem besteht nicht unbedingt darin, dass das Chemikalieneinspritzventil selbst nicht funktioniert.
In den letzten Jahren gab es im Zusammenhang mit Leitungen zur chemischen Injektion im Bohrloch verschiedene Herausforderungen.In dieser Arbeit werden einige Beispiele aus diesen Erfahrungen gegeben.In dem Papier werden Herausforderungen und Maßnahmen zur Lösung der Probleme im Zusammenhang mit DHCI-Leitungen erörtert.Es werden zwei Fallbeispiele angegeben;eine zum Thema Korrosion und eine zum Thema Chemical Gun King.Es werden Felderfahrungen besprochen, die die Komplexität kontinuierlicher Bohrlochinjektionssysteme im Hinblick auf Niederschlags- und Korrosionsprobleme zeigen.
Auch Laborstudien und die Anwendung neuer Methoden zur chemischen Qualifizierung werden berücksichtigt;wie man die Chemikalie pumpt, Ablagerungspotenzial und -verhinderung, komplexe Geräteanwendung und wie sich die Chemikalie auf das obere System auswirkt, wenn die Chemikalie wieder produziert wird.Zu den Annahmekriterien für die chemische Anwendung gehören Umweltaspekte, Effizienz, Speicherkapazität auf der Oberseite, Pumpengeschwindigkeit, ob eine vorhandene Pumpe verwendet werden kann usw. Technische Empfehlungen müssen auf der Flüssigkeits- und Chemiekompatibilität, der Rückstandserkennung, der Materialkompatibilität, dem Design der Unterwasserversorgungsleitungen und dem chemischen Dosierungssystem basieren und Materialien im Umfeld dieser Linien.Die Chemikalie muss möglicherweise hydratisiert werden, um ein Verstopfen der Injektionsleitung durch das Eindringen von Gas zu verhindern, und die Chemikalie darf während des Transports und der Lagerung nicht gefrieren.In den bestehenden internen Richtlinien gibt es eine Checkliste, welche Chemikalien an welcher Stelle im System eingesetzt werden dürfen. Physikalische Eigenschaften wie die Viskosität sind wichtig.Das Injektionssystem kann eine Entfernung von 3 bis 50 km zur Nabelschnur unter dem Meer und eine Entfernung von 1 bis 3 km in das Bohrloch erfordern.Daher ist auch die Temperaturstabilität wichtig.Möglicherweise muss auch die Bewertung nachgelagerter Effekte, z. B. in Raffinerien, in Betracht gezogen werden.
Chemische Injektionssysteme im Bohrloch
Kosten-Nutzen
Die kontinuierliche Injektion von Ablagerungsinhibitor in das Bohrloch zum Schutz des DHS vor den Produktionsrohren kann im Vergleich zum Auspressen des Bohrlochs mit Ablagerungsinhibitor kostengünstiger sein.Diese Anwendung reduziert das Potenzial für Formationsschäden im Vergleich zu Zunderquetschbehandlungen, verringert das Potenzial für Prozessprobleme nach dem Zunderquetschen und bietet die Möglichkeit, die chemische Injektionsrate vom oberen Injektionssystem aus zu steuern.Das Injektionssystem kann auch dazu verwendet werden, andere Chemikalien kontinuierlich ins Bohrloch zu injizieren und dadurch andere Herausforderungen zu reduzieren, die weiter stromabwärts der Prozessanlage auftreten könnten.
Es wurde eine umfassende Studie zur Entwicklung einer Strategie im Bohrlochmaßstab für das Feld Oseberg Süd durchgeführt.Das größte Skalenproblem war CaCO;Ablagerungen im oberen Schlauch und möglicher DHSV-Ausfall.Die Überlegungen zur Oseberg S- oder Scale-Management-Strategie kamen zu dem Schluss, dass DHCI über einen Zeitraum von drei Jahren die kosteneffizienteste Lösung in den Bohrlöchern war, in denen die Chemikalieninjektionsleitungen in Betrieb waren.Der Hauptkostenfaktor im Hinblick auf die konkurrierende Technik des Scale Squeeze war das aufgeschobene Öl und nicht die chemischen/Betriebskosten.Bei der Anwendung von Ablagerungsinhibitoren beim Gaslift war der Hauptfaktor für die Chemikalienkosten die hohe Gasliftrate, die zu einer hohen SI-Konzentration führte, da die Konzentration mit der Gasliftrate in Einklang gebracht werden musste, um ein „Chemical Gun King“ zu vermeiden.Für die beiden Bohrlöcher auf Oseberg S oder die über gut funktionierende DHC I-Leitungen verfügten, wurde diese Option gewählt, um die DHS Vs vor CaCO zu schützen;Skalierung.
Kontinuierliches Einspritzsystem und Ventile
Bestehende Komplettierungslösungen mit kontinuierlichen chemischen Injektionssystemen stehen vor der Herausforderung, ein Verstopfen der Kapillarleitungen zu verhindern.Typischerweise besteht das Injektionssystem aus einer Kapillarleitung mit einem Außendurchmesser (OD) von 1/4 Zoll oder 3/8 Zoll, die an einen Oberflächenverteiler angeschlossen ist, durch den Schlauch geführt und mit der Schlauchaufhängung an der ringförmigen Seite des Schlauchs verbunden wird.Die Kapillarleitung wird mit speziellen Schlauchkragenklemmen am Außendurchmesser des Produktionsrohrs befestigt und verläuft an der Außenseite des Rohrs bis hinunter zum Chemikalien-Injektionsdorn.Der Dorn wird traditionell vor dem DHS V oder tiefer im Bohrloch platziert, um der injizierten Chemikalie ausreichend Zeit zum Verteilen zu geben und die Chemikalie dort zu platzieren, wo die Herausforderungen auftreten.
Am chemischen Injektionsventil (Abb. 2) enthält eine kleine Patrone mit einem Durchmesser von etwa 1,5 Zoll die Rückschlagventile, die verhindern, dass Bohrflüssigkeiten in die Kapillarleitung gelangen.Es ist einfach ein kleiner Teller, der auf einer Feder sitzt.Die Federkraft bestimmt und vorhersagt den Druck, der zum Öffnen des Ventilkegels vom Dichtsitz erforderlich ist.Wenn die Chemikalie zu fließen beginnt, wird der Ventilkegel von seinem Sitz abgehoben und öffnet das Rückschlagventil.
Es ist erforderlich, zwei Rückschlagventile zu installieren.Ein Ventil ist die primäre Barriere, die verhindert, dass Bohrflüssigkeiten in die Kapillarleitung gelangen.Dies hat einen relativ niedrigen Öffnungsdruck (2–15 bar). Wenn der hydrostatische Druck innerhalb der Kapillarleitung geringer ist als der Bohrlochdruck, versuchen die Bohrflüssigkeiten, in die Kapillarleitung einzudringen.Das andere Rückschlagventil hat einen atypischen Öffnungsdruck von 130–250 bar und wird als U-Rohr-Verhinderungssystem bezeichnet.Dieses Ventil verhindert, dass die Chemikalie in der Kapillarleitung ungehindert in das Bohrloch fließen kann, wenn der hydrostatische Druck in der Kapillarleitung größer ist als der Bohrlochdruck am Einspritzpunkt der Chemikalie im Förderrohr.
Zusätzlich zu den beiden Rückschlagventilen gibt es normalerweise einen Inline-Filter. Dieser soll sicherstellen, dass keinerlei Fremdkörper die Dichtigkeit der Rückschlagventilsysteme gefährden.
Die Abmessungen der beschriebenen Rückschlagventile sind eher klein und die Sauberkeit der eingespritzten Flüssigkeit ist für ihre Betriebsfunktion von entscheidender Bedeutung.Es wird angenommen, dass Schmutz im System weggespült werden kann, indem die Durchflussrate innerhalb der Kapillarleitung erhöht wird, sodass sich die Rückschlagventile willkürlich öffnen.
Wenn das Rückschlagventil öffnet, nimmt der fließende Druck schnell ab und breitet sich entlang der Kapillarleitung aus, bis der Druck wieder ansteigt.Das Rückschlagventil schließt dann, bis der Chemikalienfluss ausreichend Druck aufbaut, um das Ventil zu öffnen.Die Folge sind Druckschwankungen im Rückschlagventilsystem.Je höher der Öffnungsdruck des Rückschlagventilsystems ist, desto kleiner wird der Strömungsquerschnitt, wenn das Rückschlagventil öffnet, und das System versucht, Gleichgewichtsbedingungen zu erreichen.
Die Chemieeinspritzventile haben einen relativ geringen Öffnungsdruck;und sollte der Schlauchdruck am Chemikalieneinlasspunkt unter die Summe aus hydrostatischem Druck der Chemikalien in der Kapillarleitung und dem Öffnungsdruck des Rückschlagventils sinken, entsteht im oberen Teil der Kapillarleitung nahezu Vakuum oder Vakuum.Wenn die Injektion der Chemikalie stoppt oder der Fluss der Chemikalie gering ist, treten im oberen Abschnitt der Kapillarleitung nahezu Vakuumbedingungen auf.
Die Höhe des Vakuums hängt vom Bohrlochdruck, dem spezifischen Gewicht der eingespritzten Chemikalienmischung innerhalb der Kapillarleitung, dem Öffnungsdruck des Rückschlagventils am Einspritzpunkt und der Durchflussrate der Chemikalie innerhalb der Kapillarleitung ab.Die Bohrlochbedingungen variieren im Laufe der Lebensdauer des Feldes und daher variiert auch die Vakuumgefahr im Laufe der Zeit.Es ist wichtig, sich dieser Situation bewusst zu sein, um die richtigen Überlegungen und Vorsichtsmaßnahmen zu treffen, bevor die erwarteten Herausforderungen auftreten.
Zusammen mit niedrigen Injektionsraten kommt es typischerweise zu einer Verdunstung der bei solchen Anwendungen verwendeten Lösungsmittel, was zu Auswirkungen führt, die noch nicht vollständig erforscht sind.Bei diesen Effekten handelt es sich um Ausfällungen von Feststoffen, zum Beispiel Polymeren, wenn das Lösungsmittel verdunstet.
Darüber hinaus können in der Übergangsphase zwischen der Flüssigkeitsoberfläche der Chemikalie und der dampfgefüllten, nahezu vakuumnahen Gasphase darüber galvanische Zellen gebildet werden.Dies kann aufgrund der unter diesen Bedingungen erhöhten Aggressivität der Chemikalie zu lokaler Lochfraßkorrosion innerhalb der Kapillarleitung führen.Flocken oder Salzkristalle, die sich beim Austrocknen als Film innerhalb der Kapillarleitung bilden, können die Kapillarleitung verstopfen oder verstopfen.
Nun, Barriere-Philosophie
Bei der Entwicklung robuster Bohrlochlösungen verlangt Statoil, dass die Bohrlochsicherheit jederzeit während der Lebensdauer des Bohrlochs gewährleistet ist.Daher verlangt Statoil, dass zwei unabhängige Bohrlochbarrieren intakt sind.Abb. 3 zeigt das Schema einer atypischen Bohrlochbarriere, wobei die blaue Farbe die primäre Bohrlochbarrierehülle darstellt;in diesem Fall der Produktionsschlauch.Die rote Farbe stellt die sekundäre Barrierehülle dar;das Gehäuse.Auf der linken Seite der Skizze ist die Chemikalieninjektion als schwarze Linie mit dem Injektionspunkt zum Produktionsrohr im rot markierten Bereich (sekundäre Barriere) dargestellt.Durch die Einführung chemischer Injektionssysteme in das Bohrloch werden sowohl die primäre als auch die sekundäre Bohrlochbarriere gefährdet.
Fallgeschichte zum Thema Korrosion
Ablauf der Ereignisse
In einem von Statoil betriebenen Ölfeld auf dem norwegischen Kontinentalschelf wurde eine chemische Injektion eines Ablagerungsinhibitors in ein Bohrloch angewendet.In diesem Fall war der verwendete Kalkschutz ursprünglich für die Anwendung auf der Oberfläche und unter Wasser geeignet.Nach der Wiedervervollständigung des Bohrlochs erfolgte die Installation von DHCIpointat2446mMD, Abb. 3.Die Injektion des oberseitigen Ablagerungsinhibitors in das Bohrloch wurde ohne weitere Tests der Chemikalie begonnen.
Nach einem Betriebsjahr wurden Leckagen im Chemikalieneinspritzsystem festgestellt und Untersuchungen eingeleitet.Die Leckage wirkte sich nachteilig auf die Brunnenbarrieren aus.Ähnliche Ereignisse ereigneten sich bei mehreren Bohrlöchern, von denen einige während der laufenden Untersuchung geschlossen werden mussten.
Die Produktionsrohre wurden gezogen und im Detail untersucht.Der Korrosionsangriff beschränkte sich auf eine Seite der Rohre und einige Rohrverbindungen waren so korrodiert, dass tatsächlich Löcher entstanden.Ungefähr 8,5 mm dicker 3 % Chromstahl war in weniger als 8 Monaten zerfallen.Die Hauptkorrosion trat im oberen Abschnitt des Bohrlochs auf, vom Bohrlochkopf bis in etwa 380 m MD, und die am stärksten korrodierten Rohrverbindungen wurden bei etwa 350 m MD gefunden.Unterhalb dieser Tiefe wurde kaum oder keine Korrosion beobachtet, es wurden jedoch viele Ablagerungen an den Außendurchmessern der Rohre gefunden.
Das 9-5/8''-Gehäuse wurde ebenfalls zerschnitten und gezogen, und es wurden ähnliche Effekte beobachtet;mit Korrosion nur im oberen Bereich des Brunnens auf einer Seite.Das verursachte Leck wurde durch das Platzen des geschwächten Abschnitts des Gehäuses verursacht.
Das Material der chemischen Einspritzleitung war Alloy 825.
Chemische Qualifikation
Chemische Eigenschaften und Korrosionstests sind wichtige Schwerpunkte bei der Qualifizierung von Ablagerungsinhibitoren, und der eigentliche Ablagerungsinhibitor wurde mehrere Jahre lang qualifiziert und in Über- und Unterwasseranwendungen eingesetzt.Der Grund für die Anwendung der eigentlichen Chemikalie im Bohrloch waren verbesserte Umwelteigenschaften durch den Ersatz der vorhandenen Chemikalie im Bohrloch. Der Kesselsteinhemmer wurde jedoch nur bei Umgebungstemperaturen an der Oberfläche und am Meeresboden (4–20 °C) verwendet.Bei der Injektion in das Bohrloch konnte die Temperatur der Chemikalie bis zu 90 °C betragen, bei dieser Temperatur wurden jedoch keine weiteren Tests durchgeführt.
Erste Korrosivitätstests wurden vom Chemikalienlieferanten durchgeführt und die Ergebnisse zeigten 2–4 mm/Jahr für Kohlenstoffstahl bei hohen Temperaturen.In dieser Phase war die materielle technische Kompetenz des Betreibers nur minimal beteiligt.Später wurden vom Betreiber neue Tests durchgeführt, die zeigten, dass der Kesselsteinhemmer stark korrosiv auf die Materialien in den Produktionsrohren und im Produktionsgehäuse wirkte und die Korrosionsraten 70 mm/Jahr überstiegen.Das Material der chemischen Einspritzleitung Alloy 825 wurde vor der Einspritzung nicht gegen den Ablagerungshemmer getestet.Die Bohrlochtemperatur kann 90 °C erreichen und unter diesen Bedingungen sollten entsprechende Tests durchgeführt worden sein.
Die Untersuchung ergab außerdem, dass der Kalkschutz als konzentrierte Lösung einen pH-Wert von <3,0 aufwies.Der pH-Wert wurde jedoch nicht gemessen.Später zeigte der gemessene pH-Wert einen sehr niedrigen Wert von pH 0-1.Dies verdeutlicht die Notwendigkeit von Messungen und Materialüberlegungen zusätzlich zu den vorgegebenen pH-Werten.
Interpretation der Ergebnisse
Die Einspritzleitung (Abb. 3) ist so konstruiert, dass sie einen hydrostatischen Druck des Ablagerungsinhibitors erzeugt, der den Druck im Bohrloch am Einspritzpunkt übersteigt.Der Inhibitor wird mit einem höheren Druck injiziert als im Bohrloch.Dadurch entsteht beim Verschluss des Bohrlochs ein U-Rohr-Effekt.Das Ventil öffnet immer, wenn in der Injektionsleitung ein höherer Druck herrscht als im Bohrloch.Daher kann es zu Vakuum oder Verdunstung in der Einspritzleitung kommen.Die Korrosionsrate und das Lochfraßrisiko sind aufgrund der Verdunstung des Lösungsmittels in der Übergangszone Gas/Flüssigkeit am größten.An Coupons durchgeführte Laborexperimente bestätigten diese Theorie.Bei den Bohrlöchern, bei denen Leckagen auftraten, befanden sich alle Löcher in den Injektionsleitungen im oberen Teil der chemischen Injektionsleitung.
Abb. 4 zeigt eine Fotografie der DHC I-Linie mit erheblicher Lochfraßkorrosion.Die an den äußeren Produktionsrohren beobachtete Korrosion deutete auf eine lokale Freilegung von Ablagerungsinhibitor an der Lochfraß-Leckagestelle hin.Die Leckage wurde durch Lochfraß durch stark korrosive Chemikalien und Leckagen durch die Chemikalieneinspritzleitung in das Produktionsgehäuse verursacht.Der Kesselsteinverhinderer wurde aus der Kapillarleitung mit Löchern auf das Gehäuse und die Rohre gesprüht und es traten Undichtigkeiten auf.Etwaige Folgefolgen von Undichtigkeiten in der Einspritzleitung seien nicht berücksichtigt worden.Man kam zu dem Schluss, dass die Gehäuse- und Rohrkorrosion auf konzentrierte Ablagerungsinhibitoren zurückzuführen war, die von der löchrigen Kapillarleitung auf das Gehäuse und die Rohre gelangten (Abb. 5).
In diesem Fall fehlte es an der Einbindung von Materialkompetenzingenieuren.Die Korrosivität der Chemikalie in der DHCI-Leitung wurde nicht getestet und die sekundären Auswirkungen aufgrund von Leckagen wurden nicht bewertet;Beispielsweise ob die umgebenden Materialien einer chemischen Belastung standhalten.
Fallgeschichte des Königs der chemischen Waffen
Ablauf der Ereignisse
Die Strategie zur Ablagerungsverhinderung für ein HP HT-Feld bestand in der kontinuierlichen Injektion von Ablagerungsinhibitor vor dem Sicherheitsventil im Bohrloch.Im Bohrloch wurde ein starkes Kalziumkarbonat-Ablagerungspotenzial festgestellt.Eine der Herausforderungen waren hohe Temperaturen und hohe Gas- und Kondensatproduktionsraten bei gleichzeitig geringer Wasserproduktionsrate.Bei der Injektion von Ablagerungsinhibitor bestand die Sorge, dass das Lösungsmittel durch die hohe Gasproduktionsrate abgestreift würde und die Chemikalie an der Injektionsstelle stromaufwärts des Sicherheitsventils im Bohrloch ausströmen würde, Abb. 1.
Bei der Qualifizierung des Ablagerungsinhibitors lag der Schwerpunkt auf der Effizienz des Produkts unter HP-HT-Bedingungen, einschließlich des Verhaltens im oberen Prozesssystem (niedrige Temperatur).Das Hauptproblem war die Ausfällung des Ablagerungsinhibitors selbst in den Produktionsrohren aufgrund der hohen Gasrate.Labortests zeigten, dass Kalkinhibitor ausfallen und an der Schlauchwand haften könnte.Das Betätigen des Sicherheitsventils kann daher risikobehaftet sein.
Die Erfahrung zeigte, dass die Chemieleitung nach einigen Betriebswochen undicht war.Der Bohrlochdruck konnte am in der Kapillarleitung installierten Oberflächenmessgerät überwacht werden.Die Leitung wurde isoliert, um die Bohrlochintegrität zu gewährleisten.
Die chemische Injektionsleitung wurde aus dem Bohrloch gezogen, geöffnet und inspiziert, um das Problem zu diagnostizieren und mögliche Fehlerursachen zu finden.Wie in Abb. 6 zu sehen ist, wurde eine beträchtliche Menge Niederschlag gefunden und die chemische Analyse zeigte, dass es sich bei einem Teil davon um den Kesselsteinhemmer handelte.Der Niederschlag befand sich an der Dichtung und am Ventilkegel und das Ventil konnte nicht betätigt werden.
Der Ventilausfall wurde durch Ablagerungen im Ventilsystem verursacht, die verhinderten, dass sich die Rückschlagventile am Metallsitz festfressen.Die Trümmer wurden untersucht und es stellte sich heraus, dass es sich bei den Hauptpartikeln um Metallspäne handelte, die wahrscheinlich während des Installationsprozesses der Kapillarleitung entstanden waren.Darüber hinaus wurden an beiden Rückschlagventilen, insbesondere auf der Rückseite der Ventile, einige weiße Ablagerungen festgestellt.Dies ist die Niederdruckseite, dh die Seite, die immer mit den Bohrlochflüssigkeiten in Kontakt steht.Zunächst ging man davon aus, dass es sich dabei um Trümmer aus dem Produktionsbohrloch handelte, da die Ventile verklemmt waren und Bohrflüssigkeiten ausgesetzt waren.Die Untersuchung der Trümmer ergab jedoch, dass es sich um Polymere mit einer ähnlichen Chemie wie die als Ablagerungsinhibitor verwendete Chemikalie handelte.Dies erweckte unser Interesse und Statoil wollte die Gründe für diese in der Kapillarleitung vorhandenen Polymerreste untersuchen.
Chemische Qualifikation
In einem HP-HT-Bereich gibt es viele Herausforderungen hinsichtlich der Auswahl geeigneter Chemikalien zur Linderung der verschiedenen Produktionsprobleme.Bei der Qualifizierung des Kesselsteinhemmers für die kontinuierliche Injektion im Bohrloch wurden folgende Tests durchgeführt:
● Produktstabilität
● Thermische Alterung
● Dynamische Leistungstests
● Kompatibilität mit Formationswasser und Hydratinhibitor (MEG)
● Statischer und dynamischer Gun-King-Test
● Wiederauflösung von Informationswasser, frische Chemikalie und MEG
Die Chemikalie wird mit einer vorgegebenen Dosierungsrate injiziert,aber die Wasserproduktion wird nicht unbedingt konstant sein,dh Wasserschläge.Dazwischen die Wasserschnecken,wenn die Chemikalie in das Bohrloch gelangt,es wird von einem heißen getroffen,schnell fließender Kohlenwasserstoffgasstrom.Dies ähnelt der Injektion eines Ablagerungsinhibitors bei einer Gasliftanwendung (Fleming et al.2003). Zusammen mit
die hohe Gastemperatur,Das Risiko, dass das Lösungsmittel ausläuft, ist extrem hoch und es kann zu einer Verstopfung des Injektionsventils kommen.Dies stellt selbst bei Chemikalien, die mit Lösungsmitteln mit hohem Siedepunkt/niedrigem Dampfdruck und anderen Dampfdrucksenkern (VPDs) formuliert sind, ein Risiko dar. Im Falle einer teilweisen Verstopfung,Fluss des Formationswassers,MEG und/oder frische Chemikalien müssen in der Lage sein, die dehydrierte oder herausgeschleuderte Chemikalie zu entfernen oder wieder aufzulösen.
In diesem Fall wurde ein neuartiger Laborprüfstand entwickelt, um die Strömungsbedingungen in der Nähe der Einspritzöffnungen bei einem HP/HTg-Produktionssystem nachzubilden.Die Ergebnisse der dynamischen Gun-King-Tests zeigen, dass unter den vorgeschlagenen Anwendungsbedingungen ein erheblicher Lösungsmittelverlust zu verzeichnen war.Dies könnte zu einem schnellen „Gun King“ und schließlich zu einer Blockierung der Flusslinien führen.Die Arbeit zeigte daher, dass ein relativ großes Risiko für die kontinuierliche Injektion von Chemikalien in diese Brunnen vor der Wasserproduktion bestand, und führte zu der Entscheidung, die normalen Startverfahren für dieses Feld anzupassen und die Injektion von Chemikalien zu verzögern, bis ein Wasserdurchbruch festgestellt wurde.
Bei der Qualifizierung des Ablagerungsinhibitors für die kontinuierliche Injektion im Bohrloch lag der Schwerpunkt auf der Entfernung des Lösungsmittels und dem „Gun King“ des Ablagerungsinhibitors am Injektionspunkt und in der Fließleitung, das Potenzial für „Gun King“ im Injektionsventil selbst wurde jedoch nicht bewertet.Das Injektionsventil ist wahrscheinlich aufgrund eines erheblichen Lösungsmittelverlusts und einer schnellen Überlastung ausgefallen,Abb.6. Die Ergebnisse zeigen, dass es wichtig ist, eine ganzheitliche Sicht auf das System zu haben;Konzentrieren Sie sich nicht nur auf die Produktionsherausforderungen,aber auch Herausforderungen im Zusammenhang mit der Injektion der Chemikalie,dh Einspritzventil.
Erfahrungen aus anderen Bereichen
Einer der ersten Berichte über Probleme mit chemischen Injektionsleitungen über große Distanzen stammte von den Gull-Fak-SandVig-Dis-Satellitenfeldern (Osa et al. 2001). Die Unterwasser-Injektionsleitungen waren aufgrund des Eindringens von Gas aus den produzierten Flüssigkeiten von der Hydratbildung innerhalb der Leitung blockiert über das Einspritzventil in die Leitung eingespeist.Es wurden neue Richtlinien für die Entwicklung von Unterwasser-Produktionschemikalien entwickelt.Zu den Anforderungen gehörten die Partikelentfernung (Filtration) und die Zugabe von Hydratinhibitoren (z. B. Glykol) zu allen wasserbasierten Kalkinhibitoren, die an den Unterwasserschablonen injiziert werden sollen.Chemische Stabilität,Viskosität und Kompatibilität (Flüssigkeit und Materialien) wurden ebenfalls berücksichtigt.Diese Anforderungen wurden weiter in das Statoil-System übernommen und umfassen die Injektion von Chemikalien ins Bohrloch.
Während der Entwicklungsphase des Feldes Oseberg S oder wurde beschlossen, dass alle Bohrlöcher mit DHC I-Systemen fertiggestellt werden sollten (Fleming et al. 2006). Ziel war die Vermeidung von CaCO;Ablagerungen im oberen Schlauch durch SI-Injektion.Eine der größten Herausforderungen bei den chemischen Injektionsleitungen bestand darin, eine Verbindung zwischen der Oberfläche und dem Auslass im Bohrloch herzustellen.Der Innendurchmesser der chemischen Injektionsleitung verengte sich aus Platzgründen um das Ringsicherheitsventil herum von 7 mm auf 0,7 mm (ID), und die Fähigkeit der Flüssigkeit, durch diesen Abschnitt transportiert zu werden, hatte Einfluss auf die Erfolgsquote.Mehrere Plattformbrunnen hatten verstopfte chemische Injektionsleitungen,aber der Grund wurde nicht verstanden.Züge verschiedener Flüssigkeiten (Glykol,grob,Kondensat,Xylol,Kesselsteinhemmer,Wasser usw.) wurden im Labor auf Viskosität und Verträglichkeit getestet und vorwärts und rückwärts gepumpt, um die Leitungen zu öffnen;Jedoch,Der Zielstein-Inhibitor konnte nicht bis zum Chemikalieneinspritzventil gepumpt werden.Weiter,Komplikationen traten bei der Ausfällung des Phosphonat-Ablagerungsinhibitors zusammen mit restlicher CaCl-Z-Vervollständigungssole in einem Bohrloch und dem Übermaß des Ablagerungsinhibitors in einem Bohrloch mit hohem Gasölverhältnis und niedrigem Wasseranteil auf (Fleming et al. 2006).
Gewonnene Erkenntnisse
Entwicklung von Testmethoden
Die wichtigsten Lehren aus dem Versagen von DHC I-Systemen betrafen die technische Effizienz des Kesselsteininhibitors und nicht die Funktionalität und die chemische Injektion.Die Topside-Injektion und die Subsea-Injektion haben im Laufe der Zeit gut funktioniert;Jedoch,Die Anwendung wurde auf die chemische Injektion im Bohrloch ausgeweitet, ohne dass die chemischen Qualifizierungsmethoden entsprechend aktualisiert wurden.Die Erfahrung von Statoil aus den beiden vorgestellten Praxisfällen zeigt, dass die maßgebliche Dokumentation oder Richtlinien für die chemische Qualifizierung aktualisiert werden müssen, um diese Art der chemischen Anwendung einzubeziehen.Die beiden größten Herausforderungen wurden als i) Vakuum in der chemischen Injektionsleitung und ii) mögliche Ausfällung der Chemikalie identifiziert.
Es kann zu einer Verdunstung der Chemikalie in der Produktionsleitung (wie im Fall des Gun King) und in der Injektionsleitung (im Vakuumfall wurde eine vorübergehende Grenzfläche festgestellt) kommen. Es besteht die Gefahr, dass diese Niederschläge mit der Strömung bewegt werden in das Injektionsventil und weiter in das Bohrloch.Das Einspritzventil ist häufig mit einem Filter vor der Einspritzstelle ausgestattet,Das ist eine Herausforderung,Denn bei Niederschlag könnte dieser Filter verstopft sein und das Ventil versagen.
Die Beobachtungen und vorläufigen Schlussfolgerungen aus den gewonnenen Erkenntnissen führten zu einer umfassenden Laborstudie zu den Phänomenen.Das übergeordnete Ziel bestand darin, neue Qualifizierungsmethoden zu entwickeln, um ähnliche Probleme in Zukunft zu vermeiden.In dieser Studie wurden verschiedene Tests durchgeführt und mehrere Labormethoden entworfen (entwickelt), um Chemikalien im Hinblick auf die identifizierten Herausforderungen zu untersuchen.
● Filterverstopfungen und Produktstabilität in geschlossenen Systemen.
● Die Auswirkung eines teilweisen Lösungsmittelverlusts auf die Korrosivität der Chemikalien.
● Die Auswirkung eines teilweisen Lösungsmittelverlusts innerhalb einer Kapillare auf die Bildung von Feststoffen oder viskosen Pfropfen.
Bei den Tests der Labormethoden wurden mehrere potenzielle Probleme identifiziert
● Wiederholte Filterverstopfungen und schlechte Stabilität.
● Feststoffbildung nach teilweiser Verdunstung aus einer Kapillare
● PH-Änderungen aufgrund von Lösungsmittelverlust.
Die Art der durchgeführten Tests lieferte außerdem zusätzliche Informationen und Erkenntnisse über Veränderungen der physikalischen Eigenschaften von Chemikalien in Kapillaren, wenn sie bestimmten Bedingungen ausgesetzt sind,und wie sich dies von Massenlösungen unterscheidet, die ähnlichen Bedingungen ausgesetzt sind.Bei den Testarbeiten wurden auch erhebliche Unterschiede zwischen den Massenflüssigkeiten festgestellt,Dampfphasen und Restflüssigkeiten, die entweder zu einem erhöhten Niederschlagsrisiko und/oder einer erhöhten Korrosivität führen können.
Das Testverfahren zur Korrosivität der Kesselsteininhibitoren wurde entwickelt und in die maßgebliche Dokumentation aufgenommen.Für jede Anwendung mussten ausführliche Korrosivitätstests durchgeführt werden, bevor die Injektion eines Ablagerungsinhibitors durchgeführt werden konnte.Es wurden auch Gun-King-Tests der Chemikalie in der Einspritzleitung durchgeführt.
Bevor mit der Qualifizierung einer Chemikalie begonnen wird, ist es wichtig, einen Arbeitsumfang zu erstellen, der die Herausforderungen und den Zweck der Chemikalie beschreibt.In der Anfangsphase ist es wichtig, die größten Herausforderungen zu identifizieren, um die Art der Chemikalie(n) auswählen zu können, die das Problem löst.Eine Zusammenfassung der wichtigsten Akzeptanzkriterien finden Sie in Tabelle 2.
Qualifizierung von Chemikalien
Die Qualifizierung von Chemikalien umfasst sowohl Tests als auch theoretische Bewertungen für jede Anwendung.Technische Spezifikationen und Prüfkriterien müssen definiert und festgelegt werden,zum Beispiel innerhalb von HSE,Materialverträglichkeit,Produktstabilität und Produktqualität (Partikel).Weiter,der Gefrierpunkt,Viskosität und Kompatibilität mit anderen Chemikalien,Hydrathemmer,Das Formationswasser und die geförderte Flüssigkeit müssen bestimmt werden.Eine vereinfachte Liste von Testmethoden, die möglicherweise zur Qualifizierung von Chemikalien verwendet werden, ist in Tabelle 2 aufgeführt.
Kontinuierliche Fokussierung und Überwachung der technischen Effizienz,Dosierungsraten und HSE-Fakten sind wichtig.Die Anforderungen an ein Produkt können die Lebensdauer eines Feldes oder einer Prozessanlage verändern;variieren je nach Produktionsrate und Flüssigkeitszusammensetzung.Nachbereitende Aktivität mit Leistungsbewertung,Optimierungen und/oder Tests neuer Chemikalien müssen häufig durchgeführt werden, um das optimale Behandlungsprogramm sicherzustellen.
Abhängig von der Ölqualität,Wasserproduktion und technische Herausforderungen in der Offshore-Produktionsanlage,Der Einsatz von Produktionschemikalien ist möglicherweise erforderlich, um Exportqualität zu erreichen,regulatorischen Anforderungen,und die Offshore-Anlage sicher zu betreiben.Alle Felder stellen unterschiedliche Herausforderungen und die benötigten Produktionschemikalien variieren von Feld zu Feld und von Zeit zu Zeit.
Es ist wichtig, sich in einem Qualifizierungsprogramm auf die technische Effizienz von Produktionschemikalien zu konzentrieren,Es ist aber auch sehr wichtig, sich auf die Eigenschaften der Chemikalie zu konzentrieren,wie Stabilität,Produktqualität und Kompatibilität.Kompatibilität bedeutet in dieser Einstellung Kompatibilität mit den Flüssigkeiten,Materialien und andere Produktionschemikalien.Das kann eine Herausforderung sein.Es ist nicht wünschenswert, eine Chemikalie zur Lösung eines Problems zu verwenden und später herauszufinden, dass die Chemikalie zu neuen Herausforderungen beiträgt oder diese schafft.Vielleicht sind die Eigenschaften der Chemikalie und nicht die technische Herausforderung die größte Herausforderung.
Besondere Anforderungen
Besondere Anforderungen an die Filtration der zugeführten Produkte sollten für das Unterwassersystem und für die kontinuierliche Injektion im Bohrloch gelten.Siebe und Filter im chemischen Einspritzsystem sollten auf der Grundlage der Spezifikation der nachgeschalteten Ausrüstung des oberen Einspritzsystems bereitgestellt werden,Pumpen und Einspritzventile,zu den Injektionsventilen im Bohrloch.Wenn eine kontinuierliche Injektion von Chemikalien in das Bohrloch angewendet wird, sollte die Spezifikation im Chemikalieninjektionssystem auf der Spezifikation mit der höchsten Kritikalität basieren.Dies könnte der Filter am Injektionsventil im Bohrloch sein.
Herausforderungen bei der Injektion
Das Injektionssystem kann eine Entfernung von 3 bis 50 km zur Nabelschnur unter dem Meer und eine Entfernung von 1 bis 3 km in das Bohrloch erfordern.Physikalische Eigenschaften wie Viskosität und die Fähigkeit, die Chemikalien zu pumpen, sind wichtig.Wenn die Viskosität bei Meeresbodentemperatur zu hoch ist, kann es eine Herausforderung sein, die Chemikalie durch die Chemikalieninjektionsleitung in der Unterwasserversorgungsleitung und zum Unterwasserinjektionspunkt oder in das Bohrloch zu pumpen.Die Viskosität sollte der Systemspezifikation bei der erwarteten Lager- oder Betriebstemperatur entsprechen.Dies sollte im Einzelfall beurteilt werden,und wird systemabhängig sein.Die Geschwindigkeit der Chemikalieninjektion ist ein Erfolgsfaktor bei der Chemikalieninjektion.Um das Risiko einer Verstopfung der chemischen Injektionsleitung zu minimieren,Die Chemikalien in diesem System sollten hydratinhibiert sein (sofern die Gefahr einer Hydratbildung besteht).Die Verträglichkeit mit den im System vorhandenen Flüssigkeiten (Konservierungsflüssigkeit) und dem Hydratinhibitor muss geprüft werden.Stabilitätstests der Chemikalie bei tatsächlichen Temperaturen (niedrigstmögliche Umgebungstemperatur).,Umgebungstemperatur,Unterwassertemperatur,Einspritztemperatur) müssen durchlaufen werden.
Es muss auch ein Programm zum Waschen der chemischen Einspritzleitungen in einer bestimmten Häufigkeit in Betracht gezogen werden.Es kann eine vorbeugende Wirkung haben, die Chemikalieneinspritzleitung regelmäßig mit Lösungsmittel zu spülen,Glykol oder Reinigungschemikalien, um mögliche Ablagerungen zu entfernen, bevor sie sich ansammeln und zu einer Verstopfung der Leitung führen können.Die gewählte chemische Lösung der Spülflüssigkeit muss seinkompatibel mit der Chemikalie in der Einspritzleitung.
In einigen Fällen wird die chemische Injektionsleitung für mehrere chemische Anwendungen verwendet, basierend auf unterschiedlichen Herausforderungen im Laufe der Feldlebensdauer und den Flüssigkeitsbedingungen.In der anfänglichen Produktionsphase vor dem Wasserdurchbruch können die größten Herausforderungen anders sein als in der späteren Lebensphase, die oft mit einer erhöhten Wasserproduktion zusammenhängt.Der Wechsel von nichtwässrigen, lösungsmittelbasierten Inhibitoren wie Asphalt-En-Inhibitoren zu wasserbasierten Chemikalien wie Kesselsteininhibitoren kann zu Kompatibilitätsproblemen führen.Daher ist es wichtig, sich auf die Kompatibilität, Qualifikation und Verwendung von Abstandshaltern zu konzentrieren, wenn ein Chemikalienwechsel in der Chemikalieneinspritzleitung geplant ist.
Materialien
Bezüglich Materialverträglichkeit,Alle Chemikalien sollten mit Dichtungen kompatibel sein,Elastomere,Dichtungen und Baumaterialien, die im chemischen Injektionssystem und in der Produktionsanlage verwendet werden.Es sollte ein Testverfahren für die Korrosivität von Chemikalien (z. B. saurer Kesselsteinhemmer) zur kontinuierlichen Injektion ins Bohrloch entwickelt werden.Für jede Anwendung müssen erweiterte Korrosivitätstests durchgeführt werden, bevor die Injektion von Chemikalien durchgeführt werden kann.
Diskussion
Die Vor- und Nachteile einer kontinuierlichen chemischen Injektion im Bohrloch müssen bewertet werden.Die kontinuierliche Injektion von Ablagerungsinhibitor zum Schutz des DHS vor die Förderleitung ist eine elegante Methode, um das Bohrloch vor Ablagerungen zu schützen.Wie in diesem Artikel erwähnt, gibt es bei der kontinuierlichen Chemikalieninjektion im Bohrloch mehrere Herausforderungen,Um das Risiko zu verringern, ist es jedoch wichtig, die mit der Lösung verbundenen Phänomene zu verstehen.
Eine Möglichkeit, das Risiko zu verringern, besteht darin, sich auf die Entwicklung von Testmethoden zu konzentrieren.Im Vergleich zur Chemikalieninjektion von oben oder unter Wasser herrschen unten im Bohrloch andere und strengere Bedingungen.Das Qualifizierungsverfahren für Chemikalien zur kontinuierlichen Injektion von Chemikalien im Bohrloch muss diese veränderten Bedingungen berücksichtigen.Die Einstufung der Chemikalien muss anhand des Materials erfolgen, mit dem die Chemikalien in Kontakt kommen könnten.Die Anforderungen an die Kompatibilitätsqualifizierung und Tests unter Bedingungen, die den verschiedenen Bohrloch-Lebenszyklusbedingungen, unter denen diese Systeme arbeiten werden, möglichst nahe kommen, müssen aktualisiert und umgesetzt werden.Die Testmethodenentwicklung muss weiterentwickelt werden, um realistischere und repräsentativere Tests zu ermöglichen.
Zusätzlich,Das Zusammenspiel zwischen den Chemikalien und der Ausrüstung ist entscheidend für den Erfolg.Bei der Entwicklung der chemischen Injektionsventile müssen die chemischen Eigenschaften und die Position des Injektionsventils im Bohrloch berücksichtigt werden.Es sollte erwogen werden, reale Einspritzventile in die Testausrüstung einzubeziehen und im Rahmen des Qualifizierungsprogramms Leistungstests des Scale-Inhibitor- und Ventildesigns durchzuführen.Zur Qualifizierung von Kalkinhibitoren,Zuvor lag der Schwerpunkt auf den Prozessherausforderungen und der Skalenhemmung,Eine gute Kesselsteinhemmung hängt jedoch von einer stabilen und kontinuierlichen Injektion ab.Ohne eine stabile und kontinuierliche Injektion wird das Skalenpotenzial zunehmen.Wenn das Ventil zum Einspritzen des Kalkschutzmittels verstopft ist und kein Kalkschutzmittel in den Flüssigkeitsstrom eingespritzt wird,Das Bohrloch und die Sicherheitsventile sind nicht vor Kalkablagerungen geschützt, sodass eine sichere Produktion gefährdet sein könnte.Das Qualifizierungsverfahren muss sich zusätzlich zu den Prozessherausforderungen und der Effizienz des qualifizierten Ablagerungsinhibitors auch um die Herausforderungen im Zusammenhang mit der Injektion des Ablagerungsinhibitors kümmern.
Der neue Ansatz betrifft mehrere Disziplinen und die Zusammenarbeit zwischen den Disziplinen und die jeweiligen Verantwortlichkeiten müssen geklärt werden.In dieser Anwendung das Topside-Prozesssystem,Dazu gehören Unterwasservorlagen sowie Bohrlochdesign und -fertigstellungen.Interdisziplinäre Netzwerke, die sich auf die Entwicklung robuster Lösungen für chemische Injektionssysteme konzentrieren, sind wichtig und möglicherweise der Weg zum Erfolg.Die Kommunikation zwischen den verschiedenen Disziplinen ist von entscheidender Bedeutung;Besonders wichtig ist eine enge Kommunikation zwischen den Chemikern, die die Kontrolle über die verwendeten Chemikalien haben, und den Bohrlochingenieuren, die die Kontrolle über die im Bohrloch verwendete Ausrüstung haben.Um die Komplexität des gesamten Prozesses zu verstehen, ist es wichtig, die Herausforderungen der verschiedenen Disziplinen zu verstehen und voneinander zu lernen.
Abschluss
● Kontinuierliche Injektion von Ablagerungsinhibitor zum Schutz des DHS vor der Produktionsverrohrung ist eine elegante Methode, um das Bohrloch vor Ablagerungen zu schützen
● Um die identifizierten Herausforderungen zu lösen,Die folgenden Empfehlungen sind::
● Es muss ein spezielles DHCI-Qualifizierungsverfahren durchgeführt werden.
● Qualifizierungsmethode für chemische Einspritzventile
● Test- und Qualifizierungsmethoden für chemische Funktionalität
● Methodenentwicklung
● Relevante Materialprüfung
● Die multidisziplinäre Interaktion, bei der die Kommunikation zwischen den verschiedenen beteiligten Disziplinen entscheidend für den Erfolg ist.
Danksagungen
Der Autor möchte Statoil AS A für die Erlaubnis zur Veröffentlichung dieser Arbeit sowie Baker Hughes und Schlumberger für die Erlaubnis zur Verwendung des Bildes in Abb. 2 danken.
Nomenklatur
(Ba/Sr)SO4=Barium/Strontiumsulfat
CaCO3=Calciumcarbonat
DHCI = chemische Injektion im Bohrloch
DHSV = Bohrlochsicherheitsventil
zB=zum Beispiel
GOR = Gasölverhältnis
HSE = Gesundheitssicherheitsumfeld
HPHT = Hochdruck, hohe Temperatur
ID=Innendurchmesser
dh=das ist
km=Kilometer
mm=Millimeter
MEG=Monoethylenglykol
mMD = Meter gemessene Tiefe
OD = Außendurchmesser
SI=Ablagerungshemmer
mTV D=Meter vertikale Gesamttiefe
U-Rohr = U-förmiges Rohr
VPD = Dampfdruckdämpfer
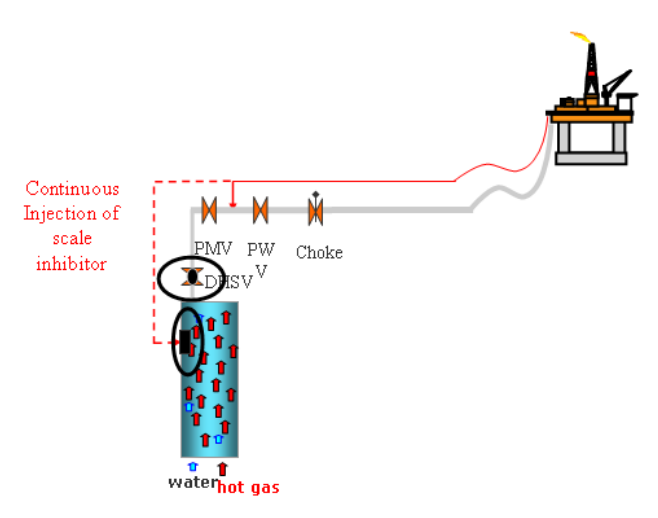
Abbildung 1. Übersicht über die chemischen Injektionssysteme unter Wasser und im Bohrloch in atypischen Bereichen.Skizze der chemischen Injektion stromaufwärts des DHSV und der damit verbundenen erwarteten Herausforderungen.DHS V=Bohrlochsicherheitsventil, PWV=Prozessflügelventil und PM V=Prozesshauptventil.
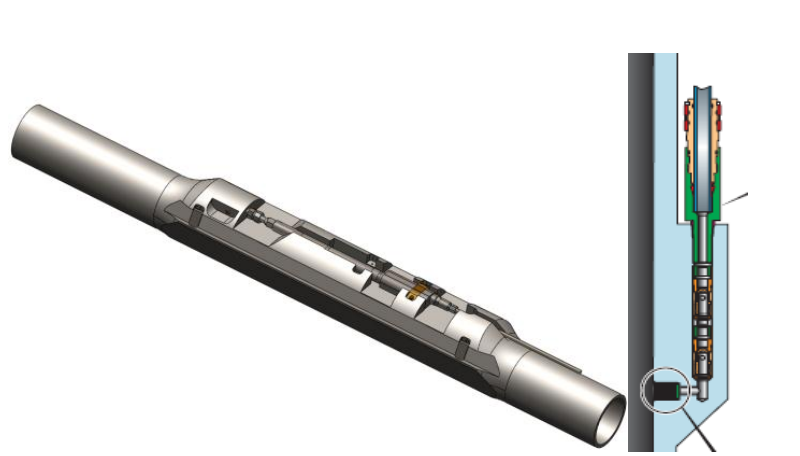
Abbildung 2. Skizze eines atypischen chemischen Injektionssystems im Bohrloch mit Dorn und Ventil.Das System wird an den Oberflächenverteiler angeschlossen, durchgeleitet und mit der Rohraufhängung an der ringförmigen Seite des Rohrs verbunden.Der chemische Injektionsdorn wird traditionell tief im Bohrloch platziert, um einen chemischen Schutz zu bieten.
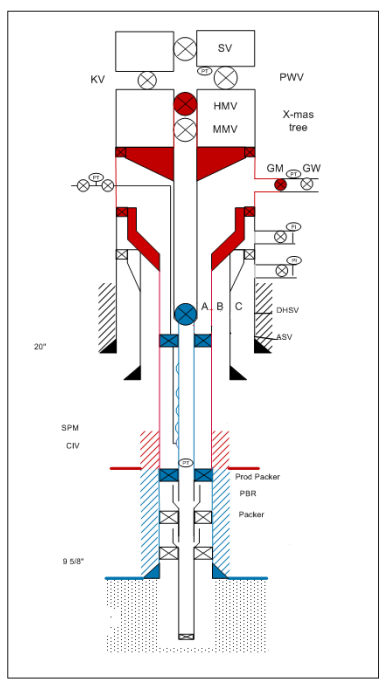
Abbildung 3. Typisches Schema einer Bohrlochbarriere,wobei die blaue Farbe die primäre Well-Barrierehülle darstellt;in diesem Fall der Produktionsschlauch.Die rote Farbe stellt die sekundäre Barrierehülle dar;das Gehäuse.Auf der linken Seite ist die chemische Injektion dargestellt, eine schwarze Linie mit dem Injektionspunkt zum Produktionsrohr im rot markierten Bereich (sekundäre Barriere).
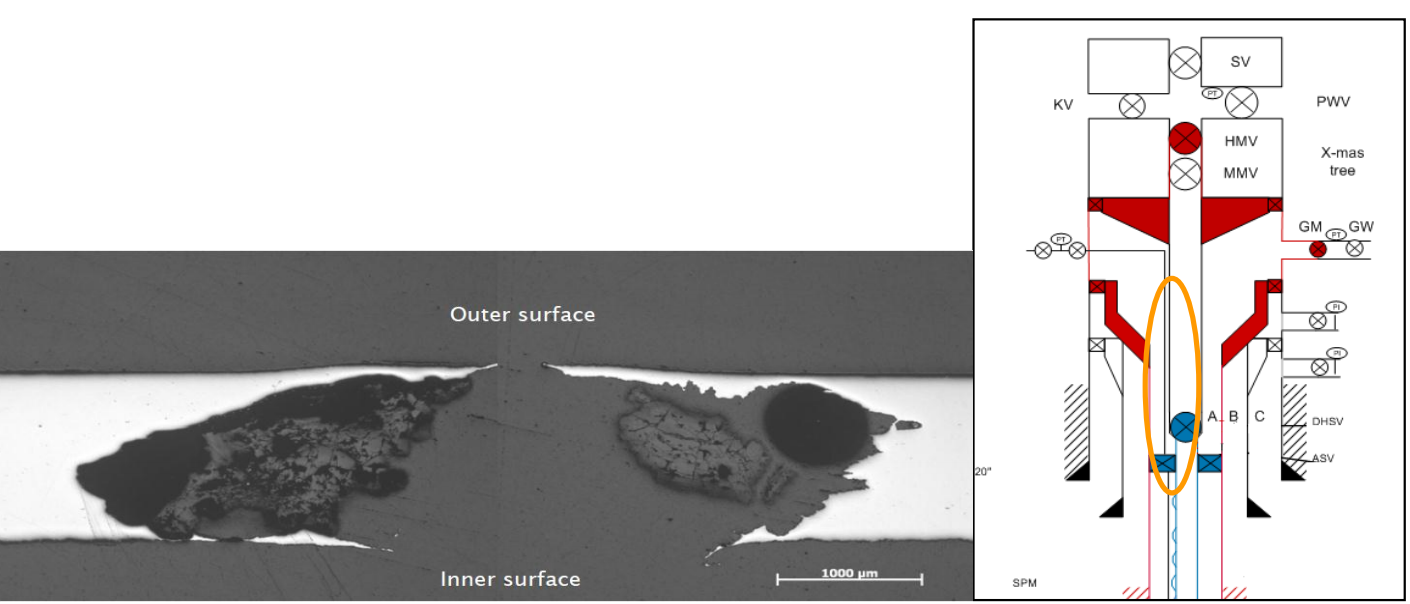
Abbildung 4. Lochfraß im oberen Abschnitt der 3/8-Zoll-Einspritzleitung.Der Bereich ist in der Skizze des atypischen Bohrlochbarrierenschemas dargestellt und mit einer orangefarbenen Ellipse markiert.
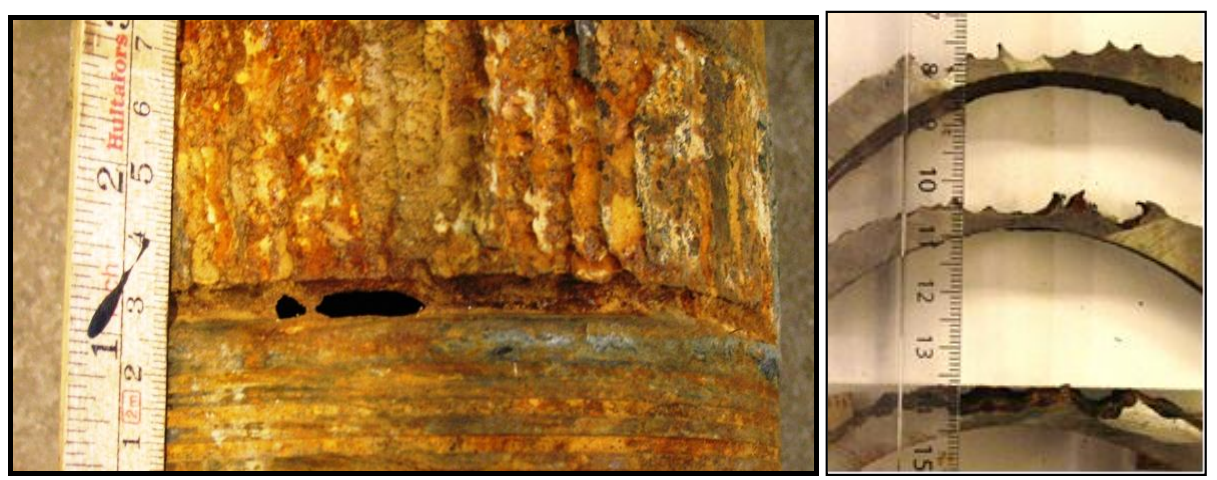
Abbildung 5. Schwerer Korrosionsangriff auf das 7-Zoll-Rohr mit 3 % Chrom.Die Abbildung zeigt den Korrosionsangriff, nachdem Kalkinhibitor aus der mit Löchern versehenen Chemikalieneinspritzleitung auf die Produktionsrohre gesprüht wurde.
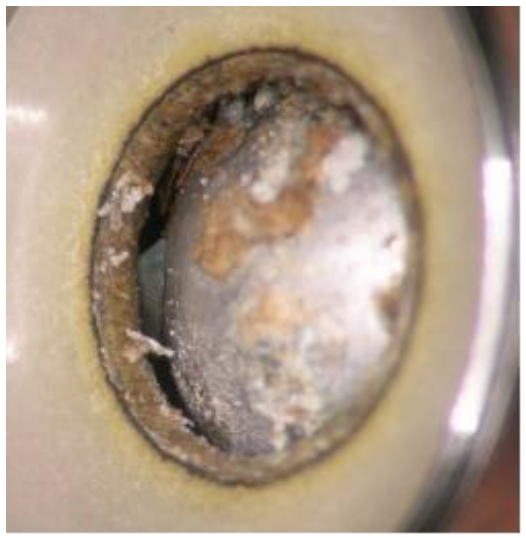
Abbildung 6. Im Chemikalieneinspritzventil gefundene Ablagerungen.Bei den Rückständen handelte es sich in diesem Fall um Metallspäne, die wahrscheinlich vom Installationsprozess stammten, zusätzlich zu einigen weißlichen Rückständen.Die Untersuchung der weißen Trümmer ergab, dass es sich um Polymere mit einer ähnlichen Chemie wie die injizierte Chemikalie handelte
Zeitpunkt der Veröffentlichung: 27. April 2022